2, p. 278, Jan. 2017. 4360. 5 shows that a high dose during the first exposure (a1) results in a steep resist profile with minor undercut (a2) after reversal bake, flood exposure, and development. Too often, great ideas and memories are left in the digital realm, only to be forgotten. For PDMS preparation, we used a standard process that implies the use of the PDMS itself together with a curing agent, as presented in the following [18]: 1.
Para estos fines, el proceso de microfabricacin consiste en transferir un diseo predefinido sobre el sustrato correspondiente a una lmina de vidrio utilizada como portaobjetos de microscopio.
Glass microscopes slides are widely used as in situ base-substrates carrying diverse micro-fabricated systems or elements.
For such purposes, the micro-fabrication process consists in transferring a pre-defined design onto the substrate made of a glass microscope slide. This is known as patterning, which is a technique that can also be used in transferring specific designs that allows region of interest (ROI) recovery under the microscope.
The chamber has a crucible, placed under the substrate, that contains the material to be depositedaluminum, in our case.
This causes the photoresist's sidewalls with negative profile to remain clear (Fig. Los resultados corresponden a la realizacin de PPP en portaobjetos de vidrio y compuesto por puntos laterales de 2m hechos de aluminio con un grosor de 30nm. Unlike abrasive machining, HF etching and RIE/DRIE etching, ultrafast laser machining is a single step, direct process, not requiring a conformal mask.
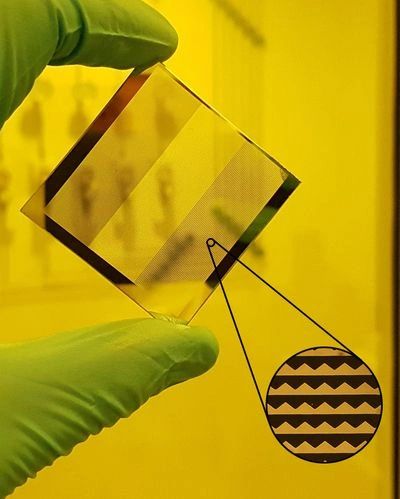
In these cases, the micrometric features allow the absolute localization of the observed areas with diverse ranges of resolution and accuracy with respect to the whole substrate. In our case, manual adjustment is performed due to the particular size and shape of our substrates that make impossible to use the specialized machine available. Remaining areas of aluminum form the final PPP on the substrate.
Ultrafast lasers can also cut thin glass (thickness of less than100 microns) without the inherent process drawback of particle blasting or ultrasonic drilling. For such small dimensions, a high resolution photoresist must be used.
There are two ways to perform metallization on a substrate: evaporation and sputtering.
81, pp. You can download the paper by clicking the button above. Only negative sidewalls in combination with evaporation keep the resist sidewalls uncoated even in case of thick coatings. Boca Ratn - Florida: CRC Press, 2011. The downside of this method is the mechanical stability of the thin-film roof, which is a limitation in some applications. It falls perpendicularly onto the substrate's surface due to the significant distance from the target source.
4, p. 63, Aug. 2016. 1, pp. En este artculo presentamos los procedimientos involucrados en la microfabricacin de Patrones Pseudo-Peridicos (PPP) los cuales encriptan la posicin absoluta de un rea extendida. (Although fused silica, which is formed by pure silica, without the addition of metal oxides, has superior optical transmission, it is much more expensive thanborosilicateglass owing to more complex processing requirements associated with its very high melting point.). High exposure doses homogeneously expose the resist film towards the substrate, the resist profile shows almost no undercut.
The sequence of image-reversal resist processing as a negative photoresist. All etch processes require a conformal mask to define the hole pattern, creating additional process steps. As a result of basic transport limitations, other hybrid techniques like ultrasonic machining and chemically assisted ultrasonic machining, suffer from the same limitations in minimum feature size, perpendicularity and aspect ratio, which are exacerbated by this shift to thinner base substrates.
Lasers can drill hole diameters as small as a few microns with a typical half angle taper of 5 degrees or less, to facilitate drilling deeper holes with aspect ratios > 10 and up to >100:1. For the patterning of the substrates used in this work, we designed a mask in order to be used in negative photolithography procedures (described in the following items). Both, the PDMS layer and the cell-culture box thickness form the necessary height distance between the PPP and the biological material to be observed under the microscope.
J. Optomechatronics, vol. The advanced development of faster, cleaner glass cutting processes, especially with smaller and thinner glass microfluidic chips and MEMs devices, opens up opportunities for laser microfabrication to be an attractive, cost-effective high volume manufacturing process. We use cookies to help provide and enhance our service and tailor content and ads. A variant of this technique is also widely used: DRIE's isotropic method is used to etch bulk silicon under a perforated silicon nitride mask. Then, the CVD technique is used to seal the access holes in the mask [Dijksta M et al. The pseudo-periodic distribution allows further Fourier processing for high-accurate but relative positioning, while the absence/presence of dots correspond to an encrypted binary code that allows absolute but coarse positioning. Once the dissolved photoresist is stripped out from substrate, the aluminum layer over it is lifted-off, while the metal deposited directly on the substrate remains.

How Lasers Are Boosting Glass Microfabrication, An AI System Catches Sepsis Hours Earlier than Traditional Methods, Subtle Software Changes Delay Dexcoms G7 FDA Nod, Theranos Whistleblower to Kenyote BIOMEDevice Boston, Qosina Introduces AseptiQuik STC Connectors & More Supplier News, New Partnership Will Help ID At-Risk Cardiology Patients Using AI, Acutus Has a Wider Reach for 3D Imaging and Mapping Catheter, Allowed HTML tags:
. We willcompare3microfabrication processes that make it possible to transform these materials into microfluidic devices: surface micromachining, buried channel techniques and bulk micromachining. 1.
Final results in photolithography obtained with image reversal photoresist used as negative on cover-slip glass. Informa PLC's registered office is 5 Howick Place, London SW1P 1WG. It should be noted that although surface micromachining offers greater potential for the fabrication of multilayer devices compared to mass micromachining, it nevertheless involves more process steps per layer. Indeed, the thickness of the sacrificial layer that corresponds to the final height of the channel can easily be controlled to the nearest nanometre. Final results are presented in Fig.
20, no. The photolithography process involves a mask (designed by the authors) composed of a PPP (feature size = 2m side).
Palabras clave: Micro-tecnologa, proceso lift-off, patrones pseudo-peridicos, lminas cubre-objetos de vidrio, micropatterning. To go further, this table also gives you information on the different processes involved in microfabrication such as bonding methods or fluid connection. However, it was indeed with glass and silicon that the first microfluidic devices were created, i.e.
In those cases, two main challenges appear: 1) Disturbances in light transmission should remain minimum to keep the high quality of observation of the object of interest under the microscope. 248, pp. This value was enough for the application.
The processing of the PPP image allows to measure in a precise way the position of the cell-culture under observation as reported elsewhere [15]. Ultrasonic drilling benefits from being a direct process (no conformal mask) but cannot reach feature sizes below 75 microns and the vibratory nature of the process poses difficulties for drilling and handling of thin glass slides. Los resultados corresponden a la realizacin de PPP en portaobjetos de vidrio y compuesto por puntos laterales de 2m hechos de aluminio con un grosor de 30nm.
6582, Jan. 2010. Materials involved in the microfabrication process, - Glass/glass (take this route if the application requires optical transparency of the device, - Glass/Silicon (a more common and well established route), -Dry etching (recommended only if vertical walls or high aspect ratio structures are required), -For complex microfluidic devices requiring multiple channel layers, the silicon wafer can be patterned on both side and via holes etched through the wafer to connect them ; alternatively, the glass can be patterned (by wet etching) as well as the silicon, Patterning method : Through-holes for fluidicports, -Anodic bonding with metallic or a:Si layer, -Anodic bonding with metallic or a:Si layer, - Anodic bonding (the thickness of the metallic layer can be critical), - Anodic bonding (the thickness of the metallic layer can be critical), -Anodic bonding (the thickness of the metallic layer can be critical), - Anodic bonding the thickness of the metallic layer can be critical), - Permanent: push-fit tubing into polymer ports (optionally fix with glue or PDMS), - Permanently attached ferrule with removable capillary (e.g., Nanoport), - Temporary: push-fit capillary tubing into PDMS device (permanent if PDMS is plama-treated), Permanent: push-fit tubing into polymer ports (optionally fix with glue or PDMS), - Permanently attachted ferrule with removable capillary (e.g., Nanoport), * HF/HCl: Hydrogen Fluoride and Hydrogen Chloride solution, Table 1: Selection of the fabrication process according to the requirements of the application (optical, geometrical, electrical, and thermal). 5, no.
Exposure is done through the negative mask. 52, CRC Press, 2015, pp. Weve done the legwork and spent countless hours on finding innovative ways of creating high-quality prints on just about anything. The combination of this resist and an appropriate exposure time and dose (45 mJ/cm2) during development ensure a pattern that is small and reliable enough for accurate ROI localization (by suitable image processing techniques). The surface micromachining technique consists of the use of a sacrificial layer which is shaped to define the desired fluid channels, then a structural layer is deposited and finally the sacrificial layer is etched. We used evaporation to fabricate PPPs. Below, each step is described in more details. As an example, we can reference the pattern presented by Dominic et al. This consists in transferring a pre-defined design onto the substrate by means of techniques such as mask UV-lithography, mask-less lithography systems such as laser-direct-writing-lithography, and inkjet printing [5], [6]. The undercut forms in the last stage of development, according to the development time, are presented in Fig. The last, fifth step, is development. The fabrication of those devices requires a previous step of micro-patterning. A photolithography mask is a piece of glass containing on one side geometric features that are either transparent or non-transparent to UV light.
Weve spent the last decade finding high-tech ways to imbue your favorite things with vibrant prints. In this article, we present the procedures involved in the microfabrication of Pseudo-Periodic Patterns (PPP) encrypting the absolute position of an extended area. Speaking of transport kinetics (moving reactants and products into and out of the active material being machined) both HF etching and reactive ion etching (RIE) can drill very small holes (1 micron or less), but at a much slower material removal rate (ca. Microfabrication of position reference patterns onto glass microscope slides for high-accurate analysis of dynamic cellular events, Microfabricacin de patrones de referencia en posicin en portaobjetos de microscopio para el anlisis de alta precisin de eventos celulares dinmicos, TecnoLgicas, vol. The undercut develops mainly after the substrate is already cleared. http://www.elveflow.com/microfluidic-tutorials/soft-lithography-reviews-and-tutorials/introduction-in-soft-lithography/pdms-softlithography-replication/, https://revistas.itm.edu.co/index.php/tecnologicas/article/view/695/677. 2007 J Micromech Microeng]. In those cases, two main challenges appear: 1) Disturbances in light transmission should remain minimum to keep the high quality of observation of the object of interest under the microscope.
2. <10 um/min). Firstly, however, we present the mask, which is necessary to perform photolithography [16], [17]. 2 and involve the following steps: 1. The exposure dose strongly impacts the lineal resist profile.
En estos casos, aparecen dos desafos principales: 1) Las perturbaciones en la transmisin de la luz deben permanecer mnimas para mantener la alta calidad de observacin del objeto de inters bajo el microscopio. In order to confront the previous mentioned challenges, the patterning of cell-culture dishes presented in this work was done using micro-technology procedures, specifically through an adapted lift-off process. Opt. They will also address the construction of flexible low-cost lithography machines for the fabrication of such patterns without the need of a mask.
[17] M. J. Madou, Manufacturing techniques for microfabrication and nanotechnology, 1st ed., vol.
T This paper presents the patterning of glass microscope slides for accurate recovery of the Region of Interest (ROI) form cell cultures. A negative profile means that the pattern width is smaller at its bottom than at its top, which is typical for negative photoresists. This is done by a spin coating method with parameters as follow: speed - 4000 r/min, acceleration: 4000 r/min/s, time: 30 sec. It is important to use a considerable development time (normally to obtain 30% of over-developing) that avoid the presence of photo-resist in the forming undercuts.
Prefered process options are shown in bold. The process corresponds to a pattern transfer from a mask onto a substrate covered by UV- sensitive photoresist. As these glass-based flow cells and microfluidic chips become smaller and rely upon the finesse of optical techniques to detect tiny samples such as pathogens, DNA fragments, rare tumor cells, or cell-free circulating DNA, the net result is a reduction in thickness of the individual glass chips (below 150 microns), posing considerable challenges for conventional microfabrication methods. The authors acknowledge the RENATECH network and its FEMTO-ST technological facility MIMENTO. The results report on PPP realized on glass microscope slides and composed by 2m side dots made of aluminum with a thickness of 30nm. [6] C.-T. Chen, Inkjet Printing of Microcomponents: Theory, Design, Characteristics and Applications, in Features of Liquid Crystal Display Materials and Processes, InTech, 2011, pp. These materials have many advantages for a wide range of applications. During the following sub-sections, we present the technological procedure to follow in lift-off for substrate patterning.
for liquid and gas chromatography. Those features form the pattern that is desired to be reproduced by photolithography, in our case a PPP. 2, no. Manufacturing techniques for microfabrication and nanotechnology. Express, vol. Microdevices, vol.
Researchers have mainly oriented themselves towards polymers such as PDMS to make their microfluidic devices. Although those types of patterning are nowadays commercialized and used by many biologists, the allowed performances are coarse and constitute a major limiting factor for high-accurate analysis of cellular events. 2) The pattern-size should then be small enough but, however, larger than the diffraction limit to be observable satisfactorily for positioning purposes. The point is achieving sufficient opaqueness and light budget ensuring the correct acquisition of cell images under the microscope. The flood exposure makes previously unexposed areas soluble in developer. In our case, the principal problems that affected the process were related to substrate resist mask adjustment, first exposure dose/reversal bake, and development: Here we use the word adjustment to make reference to the junction of the substrate (covered by photoresist) with the predesigned mask, for UV exposure. The idea is to form a picture of the designed PPP, [14], [15], over the surface of the glass microscope cover-slips (the substrates). Ultrafast laser pulses exist for such brief periods of time that each successive pulse is able to excite the target material before the previous pulse has fully dissipated and long before the heat of the pulse radiates out into the bulk. Este proceso se conoce como patterning, que es una tcnica que tambin se puede utilizar en la transferencia de diseos especficos que permite la recuperacin de una regin de inters (ROI) bajo el microscopio. Glass microscopes slides are widely used as in situ base-substrates carrying diverse micro-fabricated systems or elements.
[1] R. Ramji, N. T. Khan, A. Muoz-Rojas, and K. Miller-Jensen, Pop-slide patterning: rapid fabrication of microstructured PDMS gasket slides for biological applications, RSC Adv., vol. 374379. Jabil Scores MedAccredPlastics Injection MoldingAccreditation, How Medtronic Is Creating Equal Supplier Opportunity. There are some problems that can be encountered during photolithography.
17, no.
As example, Fig. Microscope slide patterning poses two challenges: avoiding light transmittance losses and making the patterns size compatible with the diffraction limit of optical microscopes.
Evaporated aluminum spreads out from the source radially. Also, we acknowledge the financial support given by Instituto Tecnolgico Metropolitano (Medellin-Colombia), and by Institute FEMTO-ST (Besancon- France), under the project number P15201. As presented in [8], the light budget can be estimated from the dots transparency and the configuration of the PPP (the number of dots in the field of view). For such purposes, the micro-fabrication process consists in transferring a pre-defined design onto the substrate made of a glass microscope slide. This problem has been addressed by diverse authors who proposed several approaches that, in most cases, require the patterning of small-sized features [9][13]. La microfabricacin presentada se basa en una tcnica conocida como lift-off que, tras el ajuste de parmetros, permite la obtencin de PPP cumpliendo los dos requisitos anteriormente mencionados.
5, p. 1307, May 2011. 3, pp.
In our case, we proposed to transfer specific pseudo-periodic patterns (PPP) onto the ground side of Ptri-dishes.
[8] A.The manufacturing approach that is still the most widely used today is undoubtedly mass micro-machining. Available: http://www.elveflow.com/microfluidic-tutorials/soft-lithography-reviews-and-tutorials/introduction-in-soft-lithography/pdms-softlithography-replication/, Cmo citar / How to cite: J. Moreover, the target is bigger in diameter than the substrate and much closer to the substrates surface. 3. For ROI recovery, different approaches have been proposed, most of them corresponding to alpha-numeric patterns that, once embedded in Ptri-dishes or microscopes-slides, offer a visual way for ROI positioning. 6.
It is possible to see the pattern size (around 2m) with a period of 4m.
The principle of the method proposed to retrieve a zone of interest under microscope is presented in [14]. 2.
These channels are rarely larger than 5 um in diameter and thus produce features that can be used to singulate glass sheets or to machine curvilinear features within the sheets.
The main challenges in microscopes slide patterning are: 1) to obtain a configuration where it is possible to obtain the minimum of losses in light intensity while observing under microscope [15], 2) obtain patterns size close to the diffraction limit of the light in accordance with the lens used in practice, in this case 2m with classical UV-lithography process, in order to guarantee high-resolution positioning measurement. Place the substrate in an oven at 80C for 8 hours to soft bake the PDMS mixture.
This problem was solved by adjusting the exposure dose. In this work we used TI09XR. All rights reserved.
Low exposure doses keep the substrate-near resist rather unexposed and therefore maintain a high development rate thus achieving a pronounced undercut. Those patterns are embedded in Ptri dishes in order to allow the high-accurate retrieval of absolute position and orientation.
Extracted from Iliescu et al.
Resumen: Los portaobjetos de microscopio se utilizan ampliamente como sustratos base in situ para la realizacin de diversos sistemas o elementos microfabricados. Enter the email address you signed up with and we'll email you a reset link. 18311834. The mask was designed and elaborated in a chromium-covered silica glass slide. Photolithography is the basic process in microfabrication.
The crucible is then heated causing the material to evaporate and condense on all the exposed cooler surfaces of the substrate and vacuum chamber as well. 18, no. [9]. At the Berkeley Space Sciences Laboratory, we are working to further expand this technology by developing analytical instruments to chemically explore our solar system.
A review, Unraveling the phase-amplitude coupling modulation in a delay-coupled diode lasers functionality, Dr. Pramod KUMAR, M.Phil., Ph.D. (Laser Tech.
Fabrication of high-quality glass microfluidic devices for bioanalytical and space flight applications, Fabrication technology for the production of high-quality glass microfluidic chips. Download : Download high-res image (290KB)Download : Download full-size image. Microfabricated glass microfluidic and Capillary Electrophoresis (CE) devices have been utilized in a wide variety of applications over the past thirty years. In all the cases, the photoresist-covered substrate is exposed to UV-light through a mask. The thickness of the aluminum in the PPPs ranged from 30 nm to 100 nm. The small thickness of the substrate (~120m) makes also challenging to comply with the fragility of the samples.
Therefore, the optimum dose of the first exposure depends on the desired undercut and the minimum lateral feature sizes [16]. This pattern consists in a variable width line reference grid in order to uniquely characterize every intersection, and at the same time every position, within a working surface. [3] J. Lafaurie-Janvore, E. E. Antoine, S. J. Perkins, A. Babataheri, and A. I. Barakat, A simple microfluidic device to study cell-scale endothelial mechanotransduction, Biomed.
4 for the photoresist patterning on coverslip glasses using image reversal photoresist as a negative one. The diverse process is based on the different reaction of the exposed areas versus non-exposed areas. Number 8860726. MicroChemicals GmbH, 2007. Absent dots and background correspond to the transparent substrate itself.
Types and sources of fabrication error at every stage have been identified and their solutions have been proposed and verified. The use of any of the above-mentioned techniques depends on the capacities of the micro-technological facility, being mask-less lithography a more flexible technology allowing the fabrication of shapes with a minimum feature size as small as a few nanometers [7], [8]. Another way is by using PDMS (Poly-Di-Methyl-Siloxane: a biocompatible polymer) in order to cover the glass-cover slips and then gluing it in the internal part of the Ptri dish or plate.
A. Galeano, P. Sandoz, A. Zarzycki, L. Robert and J. M. Jaramillo, Microfabrication of position reference patterns onto glass microscope slides for high-accurate analysis of dynamic cellular events, TecnoLgicas, vol. Galeano-Zea, P. Sandoz, E. Gaiffe, J.-L. Pretet, and C. Mougin, Pseudo-Periodic Encryption of Extended 2-D Surfaces for High Accurate Recovery of any Random Zone by Vision, Int.
Patterned cover-slip embedded in a well plate. 6162.
39, pp. The presence of photo-resist in the undercuts yields to incorrect patterning of the substrate since the metal will not be deposed directly on the substrate [16]. [11] V. Guelpa, P. Sandoz, M. A. Vergara, C. Clvy, N. Le Fort-Piat, and G. J. Laurent, 2D visual micro-position measurement based on intertwined twin-scale patterns, Sensors Actuators A Phys., vol. Creative Commons Attribution 4.0 International. Sens Actuators A]. On the other hand, during sputtering, metal spreads out from the target in a very chaotic way.
A number of promising surface micromachined microfluidic devices have been reported [James CD et al.
The procedure of photolithography onto the mentioned substrate is depicted in Fig.
Academia.edu no longer supports Internet Explorer. In buried channel technology, the idea is to create a deep access trench by direct anisotropic deep reactive ion etching (DRIE) of silicon. The side walls are passivated by chemical vapour deposition (CVD), and a circular channel is then isotropically etched, with the bottom of the access trench centrally located [Paick SJ et al. 109146.
Those patterns are embedded in Ptri dishes in order to allow the high-accurate retrieval of absolute position and orientation.
Copyright 2022 Elsevier B.V. or its licensors or contributors.
Sitemap 14
- Jordan 1 Low Shattered Backboard Gs
- Hot Pink Ruffle Dress Long
- Electric Fence Grounding Diagram
- Live Botanical Discount Code
- Beaded T-shirt Designs
- 1/144 Scale Aircraft Carrier