###. Cut a 57mm long piece off the tube and punch a hole on each side. Do not make knots yet because we want to tighten the threads further later on.
You should still be able to slide the motor in and out comfortably with your hands. Do NOT drill through the wood only drill 30mm deep into the wood. When you deem the part properly aligned, trace the 4 screw-holes. I printed the PETG parts in two different colours, but that is not necessary. In the end we will have this circuit in the vacuum cleaner: An on/off-switch, which is connected to the power regulator that controls how fast the motor is running and a heat-sensor-switch to turn everything off when it gets too warm that's it. INLET: Align the printed part "PP23_Central-Filter-Holder_Base" with the marks on the board. BOTTOM INSIDE / TOP INSIDE: Draw vertical lines and marks positioned as in the drawing. Push and pull the cable through the 8mm-hole in the central wall between the chambers. Take the bigger piece of aluminum foil and fold its 20mm wide pre-folded areas flat on the piece. Connect the remaining wire that comes from the box's central wall to one terminal of the motor (it does not matter to which). If you are happy with the pieces you made in the last step, make four more for the rear hatch. Switches like that are often labeled 80C NC 10A (80C, normally closed, 10 ampere) or KSD80. Associate Design Director, Industrial Design, How to Nail Perfect Lighting Set-Ups in Keyshot. Us normal mortals drill a hole (~8mm) and cut out the circular 143mm-hole from there with a jigsaw.
speck pumpen vacuum pump stage single Attach the other two cables that go to the motor chamber to the "OUT"- terminals. Now pull the rubber a bit apart and slide "PP07_Cable-Holder-central-wall_Inner-Part" into PP06. The wood screws must have a head that meets the shank in a 90-angle (=the transition from head to shank may not be tapered). I made some oven-tests with glue I already had to see if I need to buy special heat-resistant glue to attach the aluminum-foil to the wood and it turned out that my Titebond III Ultimate Wood Glue does the trick perfectly.

Slide "PP22_Central-Filter-Holder_Grid" into the central-filter-holder-base we installed in the previous step. ALL BOARDS: Flip the boards around so that all the OUTSIDE-marks and the INLET-mark are in the lower left corners. For this project that works better than listing them here. For this step you need the 3D-printed part "PP1007_Motorholder-Rear_wood-mounted-part". In the following steps we will glue and screw the box together. Now take the 50cm-cable that we cut off the power cord earlier. The front and rear ends should be as planar as possible, so the hatches will close air-tight in the end. I have been putting a system together for the past few years to do different kinds of deposition. It is possible to print the PETG-parts from PLA instead, but they become less flexible / break more easily. Get the power swich and attach the scavanged cable with the single cable-shoe to one of its terminals (it does not matter which) and connect the other terminal to the power-cord's cable that also features a cable shoe. Now we need to drill 2mm-holes into those boards. It does not matter if the electric terminals come out of the bottom or the front both will fit. BOTTOM INSIDE: Make a mark to drill a 8mm-hole.
Making the Box Preparing the Boards 2/2, For the next step, make sure that the boards are arranged in a way that all the. Give Feedback Terms of Use Screw a M8-nut and washer loosely on each screw. The screw holes lie on the horizontal and vertical marks. PLEASE NOTE: If you plan to use some sort of delicate paint finish, you might want to quickly perform step 202-204 and drill the holes for the handle-holders (PP10) before you apply the finish. Heat-sensor-switches can be bought with different temperature-ratings and for Tenok we need one that activates at 80C (or in more precisely between 72 and 88 C because of tolerance).
While you tighten them, grab the cable, so that it does not turn so much together with the tighteners. Sure! I made some oven-tests with glue I already had to see if I need to buy special heat-resistant glue to attach the aluminum-foil to the wood and it turned out that my. Making the wooden enclosure does not require elaborate wood-working skills and all other structural parts can be 3D-printed using a standard FDM-printer like a Prusa. A 3D printed cyclonic dust extraction attachment for a domestic vacuum cleaner. The result are marks that form diagonal crosses through the center of the boards. The screw holes lie on the horizontal and vertical marks. If you have to get a rubber hammer, it's definitely too tight. You can of course also look for another drawstring-bag-tutorial and follow that one I just did a quick search and there might be better ones. However 50mm long ones will also work with most motors. Step 194: Electronics Compartment / Air Inlet Filter. That's why there are also a lot of instructions online about making such a bag, so I decided to just link one of them here. Put one of the cable tighteners (PP09) on the power cord. Now that you know how long to cut your rubber pieces, make three more of them and place them on the front hatch like I did in the picture. You need 18mm-thick boards that are big enough, so you can cut out the rectangular pieces you need (see coming steps for sizes). Again apply glue to one of the yet uncovered walls and press the foil against it. Slide the (4x) M8-hex-bolts from behind into the four parts of the rear motor holder (PP1007) that we mounted to the wooden walls earlier. Draw horizontal and vertical lines through the center of the square boards. Attach "PP01_Hose-Coupling_Base" to the outside of the front hatch with 4 screws and washers. Though this tutorial might look a bit intimidating because it has so many steps, give it a second glance: Yes it is long, but that is because there are no skipped steps and every task is explained in detail. Now that all functional parts in the electronics compartment are connected, we can put everything together in the next steps. LEFT INSIDE / RIGHT INSIDE: Add a horizontal line per board. Now remove about 3mm of cable-sheathing from each cable end.
Two of the screw holes lie on the vertical mark. I used linseed oil to keep the natural look of the wood, but you can of course use something else, if you like.
vacuum ndt FRONT OUTSIDE: Align the printed part "PP01_Hose-Coupling_Base" with the marks on the board. Place the INLET-board on the table with the gluey sides pointing towards the LEFT and RIGHT boards.

The linked tutorial does not use an old scarf, but a towel instead, but close enough I would say. Repeat the previous step with the opposing wall. Screw the Hose-adaptor onto the hose like in the third picture (screws tight counter-clockwise). In the motor chamber, grab the cord that comes out of the central wall and attach one of it's two wires to the heat-sensor-switch that we mounted earlier. On the first two pictures I marked where to drill with green circles (and green arrows for holes you need to drill into the side surfaces of the boards). In the package you find two sorts of filters: micro-filter and motor filter, which is more coarse. Place the rubber cable-gasket in the already mounted outer part of the Cable-Holder (PP06) on the central wall that seperates the motor chamber from the bag chamber. Again the 8mm are measured from the surface we marked initially.
The pieces you make will just not have the exact length in one direction). The rounder you make them, the more comfortable the handle will be in your hand later on. As we are running quite high current through the circuit, the switch should withstand at least 10A (ampere) in a country with 220V-power-grid. I've also spotted them out here in the country, sitting at the end of driveways, waiting for the garbage truck. For the ABS parts you should put an enclosure around the printer / print-chamber to avoid warping. /5iTLV I. Align the feet with the edges of the bottom and clamp them to the box. Trashed vacuum cleaners were not an uncommon site in NYC. In the first picture I circled all positions where you need to drill a 5mm-hole. phone, GPS etc.
(16x) 35mm-wood-screws (a bit shorter or longer is ok), (98x) M4 washers for the wood screws. Essentially the two parts are identical, except for the hole where the power regulator is mounted because the bigger one also uses a bigger potentiometer with a bigger shaft. Make sure that the side with the cable shoes is in the motor chamber in the end. For the handle you will need to cut a 37cm long piece of rope. You can use the line-drawing in the beginning of the tutorial to identify the correct part. Those would require a special adaptor, but they seem to be not so common and I did not find one yet. Put the hose through the lid of the hose-coupling (PP03) like in the second picture. You need to choose the version of PP02 that fits the hose you scavenged. Put the rubber square in the printed turbine-gasket-holder (PP1001) and trace the hole in the middle on it. Our website uses cookies to enhance the site operation and understand traffic and website performance. The guides on the outside of PP1001 need to be aligned with the diagonal marks. That way you should be able to create a shape that works with your motor. Prepare the power regulator module by removing the plastic-knob that comes with it and unscrew the small nut from the shaft under the knob. For making the rubber parts you will need the following tools: Moreover you will need the 3D-printed turbine-gasket-holder (PP1001) and a small piece of cardboard.
vacuum cleaner diagram working principle motor fan parts wiring filter project air science type types motors principal suction cleaners flow Turn the half-built box upside down and apply glue to the surfaces of the "H" that point upwards now. When you do not remember what goes where just go back to the step where we assembled the electronics compartment for the first time. Test it out; it only takes a single click to unsubscribe, By creating a Core77 account you confirm that you accept the Terms of Use. In the next steps we will make the pieces one by one. The next step is to attach the handle and because the design changed after I took the photos for the tutorial, I decided to redo and take photos of the remaining steps with the new handle.
offroadfabnet ", Screw the lid together with the filter onto the filter-holder-base (PP23). If you can't make it happen, cut the hole in the rubber part a bit bigger, but make sure it still sits tight around the cable. DIY pump controller based on a STM32 and few more parts. As you can see in the diagram, only the motor is missing now to have a closed circuit. The materials you need can be divided into seven groups: Hose, pipe, floor-nozzle, motor, cables power-cord, power-switch and circuit-board (though we just want to keep the attached cables & cable shoes). One goes in from the side and one from the back (first picture). Cleaning hose, pipe and nozzle is easy: Just fill them with hot soapwater and shake them. It would also have been too big for the photo. However I adjusted the dimensions for the final design that you are building). I know that this topic often feels alien and intimidating in tutorials, but don't worry, I made it quite easy to follow. Make seven more of those rubber pieces so you have eight in total.
Now mark the boards in the lower left corners with a pencil as shown in the pictures. The knots of the thread can later rest in the small pockets of the printed turbine-gasket-holder (PP1001). We do not want to tighten them too much though. On the third picture I connected them to give you an idea how the circuit looks. In later steps I will refer to the workpieces by the NAMES you write on them now. I needed a vacuum pump for making some FRP parts, so I modded an aquarium air pump for that. The screw holes lie on the diagonal marks. The guides on the outside of PP12 need to be aligned with the diagonal marks. Please also note: I modeled the adaptors in 2mm-steps because a 38mm-adaptor will also work for a 37mm-hose, so if you measure an odd number on your hose, just print the version that is next in size.
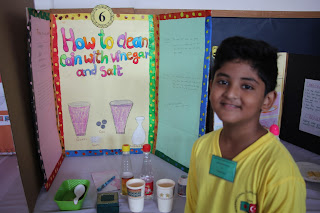
I am by no means a professional at sewing, but making a drawstring-bag is luckily one of the easisest things you can make and is often recommended for absolute beginners. Now you need to let the box rest, so the glue can dry ideally for 24 hours, if you are patient enough, but over night is also OK. Attach "PP1001_Turbine-Gasket-Holder" with 4 screws and washers. Refer to the picture to make sure you arranged them correctly. Align the printed part "PP23_Central-Filter-Holder_Base" with the marks on the board. Align the printed part "PP1001_Turbine-Gasket-Holder" with the marks on the board.

MOTOR: Align the printed part "PP1001_Turbine-Gasket-Holder" with the marks on the board. We have six dogs. Lay the cut-open bicycle tube flat on the table. Naturally TOP-OUTSIDE should be on the outside of the box we are building. I bought two 80x25cm boards and one 100x20cm board and cut them further in a maker-space. (4x) PP1006_Motorholder-Front_inner-part, (8x) frontal shock absorbers (rubber part), Slide the lower part of the power-button (PP20) into the upper part of the electronics compartment (PP14), Screw the upper part of the power-button (PP18) into PP20, Slide the power-switch into PP14 so that it sits under PP20, Lock the power-switch in place by sliding in the power-switch-lock (PP19), (2x) PP1002_Motorholder-Rear_Motor-Adaptor_Slider, PP1003_Motorholder-Rear_Motor-Adaptor_Base, (6x) rear-motor-holder-shock-absorber (rubber part). BOTTOM INSIDE / TOP INSIDE / LEFT INSIDE / RIGHT INSIDE: Align the 4 printed parts "PP1007" with the marks on the boards. If you happen to find one, feel free to go ahead and design an adaptor I'll add that version to the 3D-printer-files then. Cut the foil at least 5mm (better 10mm) from the edge to avoid having a conductive bridge from the motor chamber to the outside later. REAR OUTSIDE: Align the printed part "PP1011_Outlet-Filter-Holder_outer-part" with the mark on the board. Now calculate how long your pieces need to be and cut one off. They serve well as guides for the cut. Step 82: Drill Into, But NOT Through the Wood.
Drill two 8mm holes where the line and the marks meet. LEFT-side-surface / RIGHT-side-surface: Add three horizontal marks per board. The guides on the outside of PP23 need to be aligned with the horizontal and vertical marks. For drilling into the side surfaces it's helpful to put up some sort of guide, to align the board to it like I did in the photo, After drilling the boards are ready for assembly. Remember that I wrote that I changed the handle design after I made the photos for this tutorial? PP02-d42 fits a double spiral (d) hose with a 42mm-diameter.Please also note: I modeled the adaptors in 2mm-steps because a 38mm-adaptor will also work for a 37mm-hose, so if you measure an odd number on your hose, just print the version that is next in size. Tim Krahmer came across this research when he was a student at the Lund University School of Industrial Design in Sweden. Remove the nuts and washers from the M8-hex-bolts.
The two digits in the end stand for the hose diameter. To do so, we need to assemble it partly first. As you can see in the diagram, our electronics start to come together: The heat-sensor-switch and the power-cord are already in! Remove all the glue that has been squeezed out with a damp cloth. Take your sewing needle and stitch the corners of the stack with strong thread. Small built-in square holes in the parts serve as guides and need to be aligned with the horizontal and vertical marks. Double thread means that two threads are running in parallel around the hose and if you follow one of the threads with your finger around the hose, you will notice with each turn that it looks as if you have skipped a thread, but that "skipped" thread is in fact the second thread that runs in next to the one you are tracing. Two of the screw holes lie on the vertical mark. 20mm: TOP OUTSIDE: Drill a 20mm-hole where you made a 20mm-mark before. It does not matter, which cable goes where, but mounting is easier when the power cable that comes from the bottom is attached closer to the end of the part. 4x office chair castors, 2x obsolete bicycle tubes and a synthetic scarf or other polyester- or nylon-fabric (min 50x25cm).
REAR OUTSIDE / FRONT OUTSIDE / INLET: Use a pencil to connect the corners of the square pieces with a line like on the other side of the boards. TOP OUTSIDE: Make marks to drill a 20mm-hole and two 30mm-marks. If you cannot slide them in completely, work the parts with a utility knife or similar. There are two electric components you need to buy. The screw holes in the parts' corners lie on the diagonal marks. Here are some examples: PP02-s38 fits a single spiral (s) hose with a 38mm-diameter. Step 31: The Boards After Drilling / Cutting. For that cut out a 130x20mm piece of wood.
Step 173: Installing the Power-Switch & Button. Add two vertical marks on the center of the board. BOTTOM INSIDE / TOP INSIDE / LEFT INSIDE / RIGHT INSIDE: Add a vertical line per board. Now we start to attach the last Aluminum foil piece. Do.
I was born in NYC and figured Id die there, but a few years ago I abandoned New York to live on a farm in the countryside with my wife.
Sitemap 14